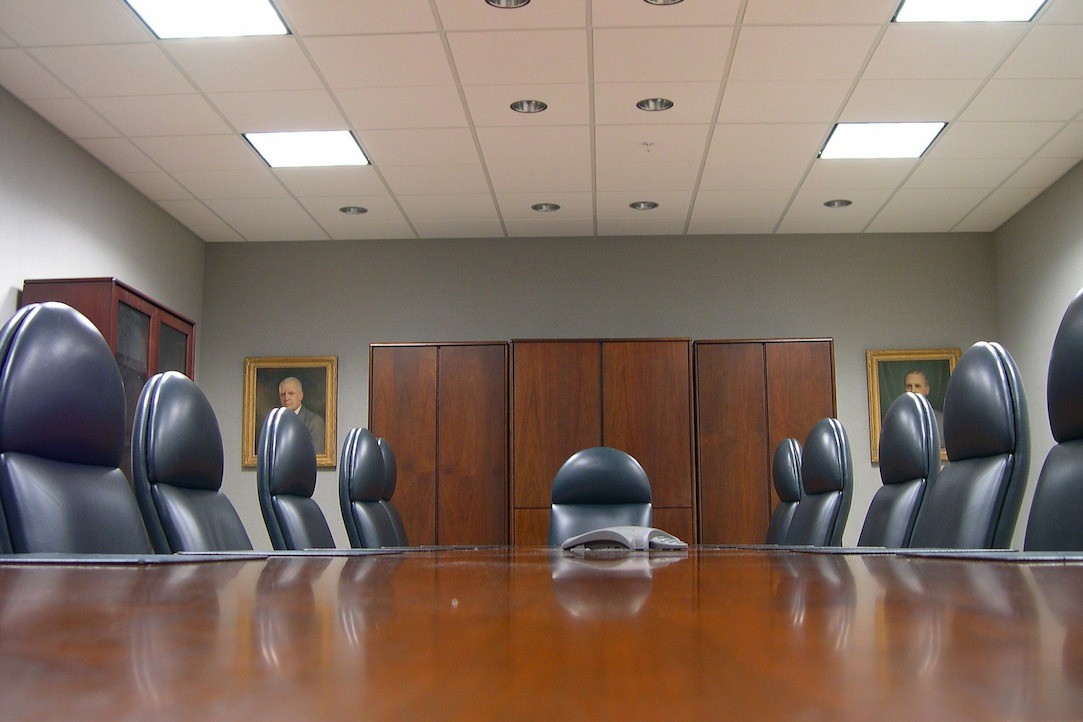
As internal auditors look ahead to end-of-year reporting deadlines, many are raising concerns that assessments may be impossible to provide or significantly delayed.
Remote work options are helping companies stay afloat in 2020; however, many elements of the audit process are more difficult in this “new normal.” Accounting standards provide guidance on reporting, but do not spell out how internal auditors gather data or conduct assessments. Many are exploring creative workarounds to access data remotely, securely, and quickly. They are looking for data points to replace the insights they usually gained from in-person visits and face-to-face conversations.
“It’s been a pretty hard five months” for auditors, BDO’s Bill Eisig told the Wall Street Journal in a report on the topic. This year, auditors are realizing they need a better understanding of risk assessments and cash flows.
Physical inventory checks, for example, typically occur before the last day of the fiscal year. Some retailers are using earlier inventory or supply counts, or have deferred counts into future months. Live video feeds and location-tracking technology are replacing on-site walk-throughs.
Remote inventory counts
Due to the coronavirus stay at home orders, conducting actual inventory counts that might be required by an internal audit can be very difficult.
In many areas right now, we are likely unable to go out to a client location and physically observe inventory like we’ve done in the past. For companies with approaching fiscal year ends, such restrictions could cause potential reporting delays.
While there are standards related to physical observation of inventory, the generally accepted procedure that has been there for years has been stood on its head when you can’t actually get to the client’s site. There are, however, a handful of alternatives available, according to AICPA Chief Auditor Bob Dohrer. They all have their pros and their cons, but it’s important for auditors to recognize that there are alternatives.
Doher recently shared some of these alternatives with the Journal of Accountancy. Some include:
Alternative Methods
Roll Forward and Roll Back: The auditor could count inventory and observe it at a point in the future when it is possible and then perform additional testing on the sales subsequent to year end as well as subsequent purchases, which probably aren’t extensive in this environment. You could effectively roll back the inventory to the year end, even if it was counted subsequent to year end. Actually, this is not an extraordinarily rare thing for auditors to do, Doher told the Journal of Accountancy.
Cycle Count Procedure: Another alternative procedure can be performed if the client is using a cycle count procedure and a perpetual inventory system. A cycle count procedure is where the client essentially has controls in place where on a periodic basis they will conduct their own test counts of just a portion of their inventory. With cycle counting, the client doesn’t perform one huge year-end, wall-to-wall count in most cases. If the auditor had been testing those controls and relying on them to establish the existence of inventory, the auditor may be able to go back to the last prior cycle count that was taken and then be able to roll forward to year end, again using sales transactions and purchase transactions and testing those during that interim period, says Doher.
Video Count: The overriding question is, can we use video to observe the inventory? And I think the answer is “yes.” I think some of the special considerations are around how well trained the personnel using the video equipment and technology are and what type of video you are going to use. There is great variety in video capabilities. A GoPro camera can be strapped to a person’s baseball cap or hard hat, and they can walk around and perform counting. A lot of warehouses also have security cameras that record and can be remotely controlled to focus in on different areas of the warehouse. That’s a different option for video. The other alternative that we’re hearing some firms are considering is a situation where client personnel go out and make a video recording of the counting of inventory. The overriding consideration when using remote video like that is that the auditor needs to have a pretty good feel for the authenticity of the video feed, says Doher.
Additional supporting evidence: There are other audit procedures that are normally performed that might lend some audit evidence about the existence of inventory. For example, inventory price-testing is performed on almost every audit, and the primary objective of inventory price-testing is, of course, to address the valuation assertion. However, you’re always looking at the quantity in the inventory, the price at which it was purchased, and what the cost was.
The bottom line is that while these are challenging times with respect to observing inventory on-site, there are ways for auditors to get sufficient, appropriate evidence about inventory that will allow them to perform a successful, high-quality audit.
Performing Remote Audits
Whether you opt for remote audits during the ongoing COVID-19 outbreak or for other reasons, there is no denying that there are some unique obstacles to overcome. Remote internal audit work may facilitate distractions, unforeseen work schedules, or even a decline in your internal audit team’s productivity. With that in mind, we have gathered some common obstacles with remote auditing below, followed by tips on how to overcome them.
Remote auditing comes with the challenge of virtual management. From coaching team members virtually to conducting the audits themselves, leaders may find themselves facing these intimidating obstacles to conquer. On the other hand, virtual management also comes with some benefits that smart internal auditors should capitalize on.